Руководство на Клапаны регулирующие игольчатые типа 10с
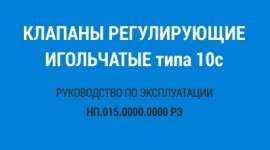
Предназначено для ознакомления с устройством и работой клапанов регулирующих игольчатых DN 20; DN 65 типа 10с НП.015.0000.0000 РЭ
Настоящее руководство по эксплуатации (далее по тексту – РЭ) предназначено для ознакомления обслуживающего персонала с устройством и работой клапанов регулирующих игольчатых типа 10с, предназначенных для регулирования расхода рабочей среды, а также, служит руководством по их
монтажу и эксплуатации.
В связи с постоянной работой по совершенствованию клапанов в конструкцию могут быть внесены незначительные изменения, не отраженные в данном РЭ.
Пример наименования при заказе изделия арматуры:
Клапан регулирующий игольчатый DN 20 1032-20-0 ТУ 2913-001-15365247-2004 .
Клапан регулирующий игольчатый с электроприводом DN 65 976-65-Э ТУ 2913-001-15365247-2004.
Содержание
- Описание и работа
- Использование по назначению
- Техническое обслуживание
- Текущий ремонт
- Назначенные показатели
- Перечень критических отказов, возможные ошибочные действия персонала, которые приводят к инциденту или аварии
- Действия персонала в случае инцидента, критического отказа или аварии
- Критерии предельных состояний
- Сведения о квалификации обслуживающего персонала
- Показатели энергетической эффективности
- Правила хранения и транспортирования
- Указания по выводу из эксплуатации и утилизации
- Диагностирование
- Комплектность
-
Наименование, местонахождение и контактная информация изготовителя
1. ОПИСАНИЕ И РАБОТА
1.1. Клапаны регулирующие игольчатые применяются для регулирования расхода рабочей среды в трубопроводе. Они устанавливаются на вспомогательных трубопроводах впрыска охлаждающей воды редукционно-охладительных установок и трубопроводах пара, работающих на параметрах, не превышающих значений, указанных в таблице 1.
Использование клапанов в качестве запорных устройств не допускается.
1.2. Клапаны со встроенным электроприводом комплектуются электроприводами ПЭМ-А32У, МЭП-25000/100-50-У-99, ПЭМ-А29У и ПЭМ-Б0У производства ОАО "АБС ЗЭиМ Автоматизация", г. Чебоксары. Также возможна комплектация с другими приводами соответствующих параметров типа А и типа Б.
Основные технические параметры приведены в таблице 1, габаритные и присоединительные размеры – в таблице 2, устройство клапанов – на рисунках 1-4, график зависимости пропускной способности от величины подъема штока – на рисунках 5-11.
1.3. Регулирование расхода воды и давления пара происходит за счет изменения площади проходного сечения кольцевой щели между седлом и штоком. Это достигается путем возвратно-поступательного перемещения штока вдоль оси потока, перпендикулярно к плоскости седла.
1.4. Клапаны игольчатые состоят из следующих узлов и деталей:
- Штампованный корпус (поз. 1);
- Шток (поз. 2) с профилированной иглой;
- Шпиндель (поз. 3);
- Грундбукса (поз. 4) и планка нажимная (поз. 5), с помощью которых обеспечивается поджатие узла сальникового уплотнения (поз. 6);
- Болты (поз. 10) для затяжки сальника;
- Бугель (поз. 7) с втулкой резьбовой (поз. 8).
Управление клапаном осуществляется с помощью рукоятки для ручного и электропривода для электроприводного исполнений (поз. 9). Соединение бугеля с корпусом резьбовое, прихвачено сваркой для фиксации.
1.5. Полное открытие клапанов производится вращением шпинделя (поз. 3) рукояткой или электроприводом (поз. 9) против часовой стрелки до упора резьбы шпинделя в резьбовую втулку (поз. 8). Закрытие клапана осуществляется вращением по часовой стрелке.
1.6. Материалы основных деталей клапанов регулирующих:
-
10с-1м, 10с-5-1(Э), 10с-5-1-2, 10с-5-2(Э), 10с-5-2-2(Э), 10с-7-3Э, 10с-5-2-1(Э), 10с-5-3(Э), 10с-5-4Э, 10с-5-4-1(Э), 10с-5-4-2(Э), 10с-3-3(Э), 584-10-0, 1032-20-0, 10с-3-3-4(Э), 976-65-М(-Э):
- Корпус – сталь 20 ГОСТ 8479-70;
- Шток – сталь 12Х18Н10Т ГОСТ 5949-75.
- 10с-6-1, 10с-6-2(Э), 10с-8-3Э, 597-10-0а, 10с-8-2, 1031-20-0, 10с-8-4, 1193-32-0, 1195-50-0(М), 1197-65-Э, 10с-6-4Э-5,0:
-
- Корпус – сталь 12Х1МФ ГОСТ 8479-70;
- Шток – сталь 20Х1М1Ф1ТР ГОСТ 20072-74.
Для всех типов клапанов:
-
- Бугель – сталь 20, 25 ГОСТ 8479-70;
- Шпиндель – сталь 40Х ГОСТ 1050-88.
1.7. При необходимости обжатия сальниковых колец крутящий момент затяжки болтов должен соответствовать значениям, указанным в таблице 4.
1.8. Порядок обжатия сальникового уплотнения
а) Провести обжатие сальникового уплотнения усилием Q, создаваемым крутящим моментом затяжки болтов в соответствии с значениями, указанными в табл. 4;
б) Сделать 5-6 циклов полного хода для распределения усилия затяжки по высоте сальникового пакета;
в) Вновь обжать сальниковый пакет усилием Q;
г) Повторить п.п. б) и в) до прекращения ослабления затяжки болтов после п. б).
Таблица 1. Основные технические параметры
- Допускается применение при температуре до Тmax = 450 °С и давлении согласно ГОСТ 356-80.
Нерегулируемый пропуск среды не более 2% от Кvу.
** Давление рабочее.
*** Максимальное усилие на штоке.
1.9. На корпусе клапана должна быть нанесена маркировка (Рисунок 12). Маркировка должна содержать следующие сведения:
- Наименование и (или) обозначение типа, марки, модели оборудования;
- Параметры и характеристики, влияющие на безопасность (давление номинальное (PN, кгс/см²) или давление рабочее (Рр, кгс/см²) и температура (t, °С));
- Диаметр номинальный;
- Наименование марки материала, из которого изготовлен корпус или условное обозначение;
- Товарный знак или наименование предприятия-изготовителя;
- Заводской номер изделия по системе нумерации предприятия – изготовителя (при Dn≥50);
- Дата изготовления;
- Сделано в России (для экспорта);
- Стрелку-указатель направления потока среды (в случае регламентированного направления среды);
- Клеймо ОТК;
- Знак обращения продукции на рынке государств-членов ТС (допускается располагать в эксплуатационной документации).
Клапаны отправляются заказчику с заглушенными патрубками и плотно закрытым затвором, упакованными в соответствии с требованиями договора, контракта, технической документации и технологических инструкций предприятия-изготовителя
Рисунок 1. Клапан регулирующий игольчатый 10с
- Корпус
- Шток
- Шпиндель
- Грундбукса
- Планка нажимная
- Кольцо сальниковое
- Бугель
- Втулка резьбовая
- Рукоятка
- Болт откидной
- Гайка
- Кольцо сальника
Рисунок 2. Клапан регулирующий игольчатый
- Корпус
- Шток
- Шпиндель
- Грундбукса
- Планка нажимная
- Кольцо сальниковое
- Бугель
- Втулка резьбовая
- Рукоятка
- Болт откидной
- Муфта шарнирная
- Муфта
- Кольцо сальника
Рисунок 3. Клапан регулирующий игольчатый с электроприводом
Номер позиции на рисунке
- Корпус
- Шток
- Шпиндель
- Грундбукса
- Планка нажимная
- Кольцо сальниковое
- Бугель
- Втулка резьбовая
- Электропривод
- Болт откидной
Рисунок 4. Клапан регулирующий игольчатый с прямоходным электроприводом
Номер позиции на рисунке
- Корпус
- Шток
- Фланец
- Грундбукса
- Планка нажимная
- Кольцо сальниковое
- Стойка
- Электропривод прямоходный
Таблица 2. Габаритные и присоединительные размеры, мм
*Угол разделки корпуса под приварку
Таблица 3. Размеры колец сальниковых (поз.6)
Рисунок 5. График зависимости пропускной способности Kv от величины подъема штока h
Рисунок 6. График зависимости пропускной способности Kv от величины подъема штока h
Рисунок 7. График зависимости пропускной способности Kv от величины подъема штока h
Рисунок 8. График зависимости пропускной способности Kv от величины подъема штока h
Рисунок 9. График зависимости пропускной способности Kv от величины подъема штока h клапана регулирующего 976-65-М
Рисунок 10. График зависимости пропускной способности Kv от величины подъема штока h клапанов регулирующих 976-65-Э и 10с-5-5Э-45
Рисунок 11. График зависимости пропускной способности Kv от величины подъема штока h клапана регулирующего 10с-6-4Э-5,0
Таблица 4. Необходимое усилие обжатия комплекта уплотнительных сальниковых колец
Рисунок 12. Место нанесения маркировки
2. ИСПОЛЬЗОВАНИЕ ПО НАЗНАЧЕНИЮ
2.1. Эксплуатационные ограничения
2.1.1. Требования безопасности на всех стадиях эксплуатации клапанов должны соответствовать Федеральным нормам и правилам в области промышленной безопасности «Правила промышленной безопасности опасных производственных объектов, на которых используется оборудование, работающее под избыточным давлением», утвержденное приказом Федеральной службы по экологическому, технологическому и атомному надзору от 25.03.2014 г. №116, Техническому регламенту Таможенного союза «О безопасности оборудования, работающего под избыточным давлением» (ТР ТС 032/2013), принятому Решением Совета Евразийской экономической комиссии от 2 июля 2013 г. №41, а также Техническому регламенту Таможенного союза «О безопасности машин и оборудования», утвержденному Решением Комиссии Таможенного союза от 18.10.2011 г. №823 (ТР ТС 010/2011).
2.1.2. Клапаны регулирующие игольчатые могут устанавливаться как на горизонтальных, так и на вертикальных участках трубопровода с направлением потока среды со стороны штока, так, чтобы направление потока совпадало со стрелкой, нанесенной на корпусе. Присоединение к трубопроводу осуществляется при помощи сварки.
2.1.3. В номинальном режиме скорость воды в трубопроводах, где установлены клапаны, составляет до 5 м/с, пара – до 60 м/с.
2.1.4. Категория размещения 1, 2, 3 по ГОСТ 15150-69; климатическое исполнение У, УХЛ, Т по ГОСТ 15150-69. Для клапанов серии 976, 10с-3, 10с-5, 10с-7-3Э, 1032-20-0, 584-10-0 – при температуре окружающей среды от -40 до +70 °С. Для клапанов 10с-6, 10с-8, 597-10-0а, 1031-20-0 – от -20 до +70 °С. Для эксплуатации при температуре ниже 0 °С проектом должен быть предусмотрен дополнительный обогрев и изоляция подводящего трубопровода для исключения замерзания рабочей среды в клапане.
2.1.5. В местах установки клапанов игольчатых должен быть обеспечен свободный доступ для их обслуживания и ремонта без вырезки из трубопровода.
2.1.6. Необходимо провести гидравлическое испытание на герметичность сальникового уплотнения.
2.1.7. Установка клапана на трубопровод производится с помощью сварки, при этом клапан должен быть плотно закрыт. Для варианта поставки клапана с электроприводом необходимо установить электропривод, произвести настройку муфты ограничения крутящего момента, путевых выключателей и проверить их срабатывание.
2.1.8. Полное открытие клапанов производится вращением рукоятки против часовой стрелки до упора головки штока в кольцо сальника, а закрытие – по часовой стрелке.
2.1.9. При наклонном или горизонтальном положении изделий с электроприводом должна быть предусмотрена дополнительная опора под электропривод.
2.2. Эксплуатация во взрывоопасной среде
2.2.1. Клапаны имеют уровень взрывозащиты Gb и допускаются к применению во взрывоопасных газовых средах в помещениях, за исключением подземных выработок шахт, рудников и их наземных строений, где вероятно возникновение взрывоопасной среды, создаваемой смесями воздуха и газов, паров, туманов.
2.2.2. В подтверждение применения во взрывоопасной среде на клапане должна быть нанесена маркировка «IIGb c 450», что означает, что клапан относится к оборудованию группы II с уровнем взрывозащиты Gb, с видом взрывозащиты «конструкционная безопасность-с» для применения во взрывоопасной газовой среде с температурой поверхности клапана до 450 °С. Температура поверхности соответствует температуре среды внутри трубопровода и определяется разработчиком проекта трубопровода из условий взрывобезопасности.
2.2.3. В случае применения клапана с электрическим приводом, последний должен быть во взрывозащищённом исполнении с соответствующим требованиям проекта уровнем защиты.
2.3. Монтаж клапанов регулирующих игольчатых
2.3.1. Монтаж клапанов должен производиться монтажной организацией согласно документации, разработанной проектно-конструкторской организацией, с учётом требований РД 153-34.1-003-01 "Сварка, термообработка и контроль трубных систем котлов и трубопроводов при монтаже и ремонте энергетического оборудования" и настоящего руководства по эксплуатации.
2.3.2. Клапаны отправляются на место монтажа с плотно закрытым затвором и заглушенными патрубками.
2.3.3. Транспортирование клапанов к месту монтажа должно производиться с соблюдением всех предосторожностей, гарантирующих защиту от поломки и повреждений.
2.3.4. Перед установкой клапанов в трубопровод при закрытом затворе необходимо снять заглушки, очистить внутренние полости клапана от возможного загрязнения. Законсервированные наружные поверхности клапана следует протереть ветошью, смоченной уайт-спиритом (нефрасом-С155/200) ГОСТ 3134-78 или нефрасом-С 50/170 ГОСТ 8505-80, затем раствором моющего дезинфицирующего средства "МДС" вид Б или В ТУ 12-РФ-938-95 или раствором моющего технического средства МС-37 ТУ РСФСР 964-92 до полного удаления консервационных смазок. После этого поверхности клапанов необходимо насухо протереть. Расконсервацию внутренних поверхностей, обработанных контактным ингибитором коррозии – загущенным раствором нитрита натрия, следует выполнить промывкой водой с использованием протирочного материала и последующей сушкой до полного удаления влаги.
2.3.5. Клапаны, имеющие внешние признаки повреждений (забитая резьба, погнутый шпиндель и др.), должны быть подвергнуты ревизии.
2.3.6. Монтаж и наладку арматуры должны осуществлять специализированные организации, имеющие статус юридического лица и организационную форму, соответствующую требованиям законодательства Российской Федерации, а также индивидуальные предприниматели (далее – специализированные организации).
2.3.7. Монтаж с применением сварки и термической обработки должен проводиться по технологии и рабочим чертежам, разработанным на основании ФНП "Требования к производству сварочных работ на опасных производственных объектах" (далее – ФНП) и РД 153–34.1–003–01 "Сварка, термообработка и контроль трубных систем котлов и трубопроводов при монтаже и ремонте энергетического оборудования" (далее – РТМ–1с).
2.3.8. При монтаже должна быть применена технология сварки, аттестованная в соответствии с установленными требованиями.
2.3.9. Для выполнения сварки должны использоваться исправные установки, аппаратура и приспособления, обеспечивающие соблюдение требований технологической документации.
2.3.10. К производству работ по сварке и прихватке элементов оборудования, предназначенных для работы под давлением, допускаются только сварщики, имеющие удостоверение на право выполнения данных сварочных работ. Сварочные работы должны выполняться исключительно в рамках видов, к которым допущен сварщик согласно удостоверению.
2.3.11. Руководство работами по сборке, сварке и контролю качества сварных соединений должно быть возложено на специалиста, прошедшего в установленном порядке аттестацию.
2.3.12. Работоспособность привода арматуры, имеющей механический или электрический привод, должна быть проверена до передачи в монтаж.
2.3.13. Трубопроводную арматуру монтировать в закрытом состоянии. Фланцевые и приварные соединения арматуры выполнять без натяжения трубопровода. Во время сварки приварной арматуры её затвор или клапан приоткрывается, чтобы предотвратить заклинивание его при нагревании корпуса. Если сварка проводится без подкладных колец, арматуру по окончании сварки можно закрыть только после ее внутренней очистки.
2.3.14. Технологическая документация должна содержать указания по технологии сварки металла (в том числе и по прихватке), применению присадочных материалов, видам и объему контроля, а также по предварительному и сопутствующему подогреву и термической обработке. Технологическая документация должна соответствовать требованиям ФНП и РТМ–1с.
2.3.15. Перед началом сварки должно быть проверено качество сборки соединяемых элементов, а также состояние стыкуемых кромок и прилегающих к ним поверхностей. При сборке не допускается подгонка кромок ударным способом или местным нагревом.
2.3.16. Подготовка кромок и поверхностей под сварку должна быть выполнена механической обработкой либо путем термической резки или строжки (кислородной, воздушно-дуговой, плазменно-дуговой) с последующей механической обработкой (резцом, фрезой, абразивным инструментом). Глубина механической обработки после термической резки (строжки) должна быть указана в технологической документации в зависимости от восприимчивости конкретной марки стали к термическому циклу резки (строжки).
2.3.17. При сборке стыковых соединений труб с односторонней разделкой кромок и свариваемых без подкладных колец и подварки корня шва смещение (несовпадение) внутренних кромок не должно превышать значений, установленных в технологической документации.
2.3.18. Кромки деталей, подлежащих сварке, и прилегающие к ним участки должны быть очищены от окалины, краски, масла и других загрязнений в соответствии с требованиями технологической документации.
2.3.19. Приварка и удаление вспомогательных элементов (сборочных устройств, временных креплений) должны быть произведены в соответствии с указаниями чертежей и технологической документации по технологии, исключающей образование трещин и закалочных зон в металле. Приварку этих элементов должен выполнять сварщик, допущенный к проведению сварочных работ на данном оборудовании.
2.3.20. Прихватка собранных под сварку элементов должна быть выполнена с использованием тех же сварочных материалов, которые будут применены (или допускаются к применению) для сварки данного соединения.
2.3.21. Прихватки при дальнейшем проведении сварочных работ удаляют или переплавляют основным швом.
2.3.22. Сварные соединения элементов с толщиной стенки более 6 мм подлежат маркировке (клеймению), позволяющей установить фамилию сварщика, выполнившего сварку. Система маркировки указывается в технологической документации. Способ маркировки должен исключать наклеп, подкалку или недопустимое утонение толщины металла и обеспечить сохранность маркировки в течение всего периода эксплуатации оборудования.
2.3.23. Необходимость и способ маркировки сварных соединений с толщиной стенки 6 мм и менее устанавливается требованиями технологической документации.
2.3.24. Сварочные материалы, применяемые для сварки при монтаже, должны соответствовать требованиям нормативной документации.
2.3.25. Марка, сортамент, условия хранения и подготовка к использованию сварочных материалов должны соответствовать требованиям технологической документации.
2.3.26. Сварочные материалы должны быть проконтролированы на соответствие требованиям нормативной документации.
2.3.27. Необходимость и режим предварительного и сопутствующего подогревов свариваемых деталей определяются технологией сварки и должны быть указаны в технологической документации. При отрицательной температуре окружающего воздуха подогрев производят в тех же случаях, что и при положительной, при этом температура подогрева должна быть выше на 50°C.
2.3.28. После сварки шов и прилегающие участки должны быть очищены от шлака, брызг металла и других загрязнений.
2.3.29. Термическая обработка элементов оборудования при монтаже проводится в случаях, установленных технологической документацией с учетом рекомендаций изготовителя, указанных в руководстве (инструкции) по эксплуатации.
2.3.30. При монтаже должна быть применена система контроля качества сварных соединений, гарантирующая выявление недопустимых дефектов, высокое качество и надежность эксплуатации этого оборудования и его элементов.
2.3.31. Методы контроля должны быть выбраны в соответствии с требованиями ФНП, РТМ–1с и указаны в технологической документации.
2.3.32. Контроль качества сварных соединений должен быть проведен в порядке, предусмотренном проектной и технологической документацией.
3. ТЕХНИЧЕСКОЕ ОБСЛУЖИВАНИЕ
3.1. К эксплуатации, ремонту и обслуживанию клапанов допускается персонал, изучивший их устройство, правила техники безопасности и требования настоящего руководства, аттестованный на право выполнения работ по обслуживанию регулирующей арматуры.
3.2. Для обеспечения безопасной работы по обслуживанию регулирующих клапанов КАТЕГОРИЧЕСКИ ЗАПРЕЩАЕТСЯ:
- эксплуатировать клапаны на параметрах, превышающих указанные в документации;
- производить работы по устранению дефектов при наличии давления в трубопроводе;
- настраивать муфту ограничения крутящего момента электропривода на величину, превышающую указанную в настоящем руководстве.
3.3. Во время открывания и закрывания клапана пользоваться дополнительными рычагами не допускается.
3.4. Полную разборку клапана проводить в следующей последовательности (см. рисунки 1-4):
а) освободить вращением шпинделя (поз. 3) упор штока (поз. 2) в корпусе (поз. 1) и ослабить затяжку комплекта уплотнительных колец (поз. 6), вращая гайки на болтах откидных (поз. 10);
б) снять элементы привода:
- рукоятку (поз. 9, рис. 1),
- муфту шарнирную (поз. 11),
- маховик (поз. 9, рис. 2),
- электропривод (поз. 9, рис. 3 и поз. 8, рис. 4);
в) разобрать узел соединения штока со шпинделем;
г) расстопорить соединение бугеля (поз. 7) с корпусом (поз. 1);
д) свинтить бугель (поз. 7) с корпуса (поз. 1);
е) вывинтить из бугеля шпиндель (поз. 3).
ж) свинтить гайки с болтов откидных поз.10 настолько, чтобы можно было освободить планку нажимную поз.5;
з) снять со штока поз.2 планку нажимную поз.5 и грундбуксу поз.4;
и) вынуть из камеры корпуса шток поз.2 с кольцом сальника поз.13 и комплектом уплотнительных сальниковых колец поз.6;
к) снять со штока комплект уплотнительных сальниковых колец и кольцо сальника.
3.5. Очистка от загрязнений и дефектация деталей
3.5.1. Все детали и сборочные единицы очистить от загрязнения и обезжирить уайт-спиритом ГОСТ 3134-78.
3.5.2. Проверить состояние уплотнительных поверхностей седла корпуса и штока. При наличии дефектов глубиной до 0,5 мм уплотнительные поверхности притереть, при необходимости устранения дефектов притиркой произвести ремонт по технологии, согласованной с изготовителем.
3.5.3. Убедиться в отсутствии коррозии на рабочей поверхности штока (шпинделя), соприкасающейся с комплектом уплотнительных сальниковых колец. При наличии коррозии глубиной более 0,1 мм шток (шпиндель) заменить.
3.5.4. Осмотреть все остальные детали: забоины, задиры, деформация трущихся поверхностей не допускается.
3.6. Сборка клапанов
3.6.1. Перед сборкой выполнить смазку всех резьбовых соединений, кроме резьб, соприкасающихся со средой, смазкой Лимол ТУ 38.301-48-54-95. Резьбовое соединение бугеля с корпусом, подшипники и детали узла перемещения шпинделя смазать смазкой «Политерм-термостойкая» ТУ 0254-046-00151742-2004.
3.6.2. При сборке клапана после ревизии уплотнение соединения «корпус-шток (шпиндель)» заменить на новое.
3.6.3. Порядок сборки:
а) установить в корпус поз.1 шток поз.2 так, чтобы он занял нижнее положение и своей уплотнительной поверхностью отцентрировался относительно уплотнительной поверхности седла корпуса;
б) надеть на шток кольцо сальника поз.13 и опустить его в камеру корпуса;
в) установить в сальниковую камеру комплект уплотнительных сальниковых колец поз.6;
г) установить грундбуксу поз.4;
д) ввинтить шпиндель поз.3 в бугель поз.7;
е) навернуть на корпус бугель поз.7 и застопорить;
ж) установить планку нажимную поз.5;
з) произвести окончательную затяжку комплекта уплотнительных сальниковых колец усилием, указанным в таблице 4, при помощи болтов откидных поз.10 гайками через планку нажимную поз.5 и грундбуксу поз.4 стандартным ключом равномерно с обеих сторон, контролируя при затяжке наличие зазоров между штоком поз.2 и планкой нажимной поз.5; после окончания затяжки грундбукса должна входить в камеру на глубину не менее 3 мм;
и) собрать узел соединения шпинделя со штоком;
к) установить и закрепить привод: рукоятку поз.9 (Рисунок 1), маховик поз.9 с муфтой шарнирной поз.11 (Рисунок 2), электроприводов;
л) убедится в правильности сборки, при этом проверить затяжку крепежа, правильное, без перекосов положения сопрягаемых деталей;
м) произвести настройку электропривода согласно эксплуатационной документации на привод;
н) проверить плавность хода двукратным открытием-закрытием клапана.
4. ТЕКУЩИЙ РЕМОНТ
5. НАЗНАЧЕННЫЕ ПОКАЗАТЕЛИ
5.1. Клапаны регулирующие игольчатые относятся к классу ремонтируемых, восстанавливаемых изделий с регламентированной дисциплиной и назначенной продолжительностью эксплуатации. При эксплуатации допускаются профилактические осмотры и, в случае необходимости, текущие ремонты изделий (замена сальникового уплотнения, смазка и т.п.), но не менее чем через 10000 часов работы изделия.
5.2. Изделия арматуры должны обеспечивать показатели надежности:
- средний срок службы до первого ремонта выемных деталей арматуры, не менее – 4 лет (30000 ч);
- средняя наработка на отказ, не менее 12000 часов.
5.3. Изделия арматуры должны обеспечивать показатели безопасности:
- назначенный срок службы корпусных деталей, не менее – 25 лет;
- назначенный срок службы выемных частей и комплектующих изделий, не менее - 10 лет (75000 ч);
- назначенный срок хранения – 3 года.
При достижении назначенных показателей эксплуатация арматуры должна быть прекращена независимо от ее технического состояния. Дальнейшая эксплуатация арматуры возможна только по решению комиссии, проведшей экспертное обследование в установленном нормативной документацией порядке.
6. ПЕРЕЧЕНЬ КРИТИЧЕСКИХ ОТКАЗОВ, ВОЗМОЖНЫЕ ОШИБОЧНЫЕ ДЕЙСТВИЯ ПЕРСОНАЛА, КОТОРЫЕ ПРИВОДЯТ К ИНЦИДЕНТУ ИЛИ АВАРИИ
Перечень возможных отказов:
- потеря прочности корпусных деталей и сварных соединений;
- потеря плотности материалов корпусных деталей и сварных соединений;
- потеря герметичности по отношению к внешней среде по уплотнениям неподвижных (прокладочных и беспрокладочных) соединений корпусных деталей, подвижных соединений (сальников, сильфонов, мембран и др.);
- потеря герметичности клапана (наличие утечек в клапане, превышающих установленные нормы по условиям эксплуатации);
- невыполнение функций “открытие” или “закрытие”;
- несоответствие времени срабатывания (открытие, закрытие);
- увеличение крутящего момента на открытие или закрытие арматуры более 10% от установленной в РЭ величины.
Критичность отказа (в соответствии с ГОСТ Р 55018-2012) определяет проектировщик системы, в которой применяют арматуру, в зависимости от вероятности (частоты) проявления отказа и тяжести его последствий на месте эксплуатации. Анализ видов, последствий и критичности отказов проводят в соответствии с ГОСТ Р 51901.12 или ГОСТ 27.310.
Ошибочные действия персонала, которые приводят к инциденту или аварии:
- допуск к обслуживанию арматуры неподготовленного специально персонала;
- превышение назначенных в паспорте на арматуру параметров эксплуатации;
- использование при обслуживании и ремонте материалов, не соответствующих требованиям, установленным изготовителем, и нарушение нормативных требований к разборке и сборке арматуры;
- производство работ по устранению дефектов и обжатию уплотнений, а также любую “сборку-разборку” клапана при наличии давления в трубопроводе;
- нарушение условий эксплуатации, установленных изготовителем;
- использование арматуры не по назначению.
7. ДЕЙСТВИЯ ПЕРСОНАЛА В СЛУЧАЕ ИНЦИДЕНТА, КРИТИЧЕСКОГО ОТКАЗА ИЛИ АВАРИИ
При возникновении аварийной ситуации, связанной с угрозой для обслуживающего (эксплуатирующего) персонала, должно быть произведено отключение подачи среды на клапан с последующим определением причины инцидента/аварии и принятием решения о возможности ремонта и последующей эксплуатации.
В случае достижения предельного состояния – вывод из эксплуатации и утилизация.
8. КРИТЕРИИ ПРЕДЕЛЬНЫХ СОСТОЯНИЙ
8.1. К критериям предельного состояния арматуры относятся:
• начальная стадия нарушения целостности корпусных деталей (потение, капельная течь, газовая течь);
• недопустимое изменение размеров элементов по условиям прочности и функционирования арматуры;
• потеря герметичности в разъемных соединениях, не устранимая их подтяжкой расчетным крутящим моментом;
• возникновение трещин на основных деталях арматуры;
• увеличение крутящего момента при управлении арматурой до значений выше норм.
Предельные состояния арматуры предшествуют ее отказам.
9. СВЕДЕНИЯ О КВАЛИФИКАЦИИ ОБСЛУЖИВАЮЩЕГО ПЕРСОНАЛА
В круг лиц, относящихся к персоналу, влияющему на безопасность эксплуатации арматуры, входят лица, занятые в проектировании, изготовлении, контроле качества и испытаниях, монтаже, наладке, эксплуатации, ремонте и техническом диагностировании.
В отношении всего персонала, относящегося к этому кругу, действуют требования к квалификации в соответствии с осуществляемыми функциями, изложенными в должностных инструкциях и инструкциях по профессиям.
Для специалистов и руководителей обязательна проверка знаний требований промышленной безопасности и охраны недр, установленных в федеральных законах, законодательных и иных актах РФ по общим вопросам промышленной безопасности. В инструкциях по профессиям должны быть определены требования к квалификации, здоровью и возрастные ограничения (для случаев, где это необходимо).
К производству работ по сварке и прихватке арматуры допускаются руководители сварочных работ и сварщики, прошедшие аттестацию в соответствии с «Правилами аттестации сварщиков и специалистов сварочного производства (ПБ 03-273-99)» и имеющие удостоверение на право выполнения данных сварочных работ.
К производству работ по визуально-измерительному, ультразвуковому, радиографическому, капиллярному и магнитному контролю арматуры в процессе производства, монтажа и эксплуатации допускаются специалисты, прошедшие аттестацию в соответствии с ПБ 03-440-02, и имеющие удостоверение на право выполнения данных работ.
Рабочие всех профессий, участвующие в процессе обслуживания арматуры, выполняют работу только соответствующей квалификации, перед выполнением операции проходят ознакомление с технологическим процессом и требованиями конструкторской документации.
10. ПОКАЗАТЕЛИ ЭНЕРГЕТИЧЕСКОЙ ЭФФЕКТИВНОСТИ
Основными показателями энергетической эффективности клапанов регулирующих являются коэффициент расхода среды m и условная пропускная способность клапана k, приведенные в табл. 1 настоящего РЭ.
11. ПРАВИЛА ХРАНЕНИЯ И ТРАНСПОРТИРОВАНИЯ
11.1. Условия хранения и транспортирования клапанов в части воздействия климатических факторов внешней среды должны соответствовать ГОСТ 15150-69:
• условия хранения – 6;
• условия транспортирования – по условиям хранения 9.
11.2. Хранение должно производиться при соблюдении следующих условий:
• клапаны должны храниться в закрытом сухом помещении на специальных стеллажах или в ящиках;
• патрубки должны быть заглушены;
• консервация поверхностей должна производиться в соответствии с требованиями ГОСТ 9.014-78 (группа 1-2, условия транспортирования ОЖ, вариант защиты ВЗ-1, вариант упаковки ВУ-9);
• при длительном хранении клапаны необходимо периодически осматривать, заменять по мере надобности противокоррозионную смазку и удалять обнаруженные загрязнения и ржавчину;
• срок переконсервации – 3 года.
11.3. Условия транспортирования должны обеспечивать сохранность клапанов, тары, упаковки.
11.4. Транспортирование изделия может производиться всеми видами транспорта в крытых и открытых транспортных средствах. Условия транспортирования в части воздействия механических факторов должны соответствовать условиям Ж ГОСТ 23170-78.
11.5. В период транспортирования и хранения должен осуществляться контроль за наличием заглушек, предохраняющих внутренние поверхности клапанов от загрязнений.
12. УКАЗАНИЯ ПО ВЫВОДУ ИЗ ЭКСПЛУАТАЦИИ И УТИЛИЗАЦИИ
12.1. По окончании срока службы клапанов необходимо провести их утилизацию, руководствуясь нижеперечисленными рекомендациями.
12.2. Рекомендации не распространяются на электроприводы, путевые выключатели, двигатели, подшипники.
12.3. Арматура подлежит утилизации после принятия решения о невозможности или нецелесообразности ее капитального ремонта или недопустимости ее дальнейшей эксплуатации.
12.4. Лица, ответственные за утилизацию, должны обеспечить соответствие процесса утилизации арматуры требованиям настоящего руководства.
12.5. Утилизацию арматуры необходимо производить способом, исключающим возможность её восстановления и дальнейшей эксплуатации.
12.6. При выводе из эксплуатации арматура должна быть полностью отключена от действующего оборудования, освобождена от заполняющей её среды.
12.7. Утилизация арматуры должна проводиться в соответствии с действующей НТД.
12.8. Соответствие выведения из эксплуатации и утилизации арматуры требованиям соответствующих технических регламентов обеспечивается назначаемым в эксплуатирующей организации лицом, ответственным за утилизацию.
12.9. Ответственность за принятие мер по предотвращению недопустимого использования (эксплуатации) арматуры, выведенной из эксплуатации, возлагается на эксплуатирующую организацию.
13. ДИАГНОСТИРОВАНИЕ
13.1. Техническое диагностирование в рамках экспертизы промышленной безопасности оборудования под давлением проводит специализированная организация, имеющая лицензию на проведение экспертизы промышленной безопасности, в следующих случаях:
а) по истечении назначенного срока службы или при выработке назначенного ресурса (по времени или количеству циклов нагружения);
б) при обнаружении экспертами в процессе осмотра оборудования дефектов, вызывающих сомнение в прочности конструкции, или дефектов, причину которых установить затруднительно;
д) в иных случаях, определяемых руководителем организации, проводящей экспертизу, по согласованию с эксплуатирующей организацией.
13.2. Техническое диагностирование оборудования под давлением включает следующие мероприятия:
а) анализ технической, эксплуатационной документации, содержащей информацию о техническом состоянии и условиях эксплуатации;
б) анализ результатов контроля металла и сварных соединений;
в) анализ результатов исследования структуры и свойств металла для оборудования, работающего в условиях ползучести;
г) расчет на прочность с оценкой остаточного ресурса и (или) остаточного срока службы, а также при необходимости циклической долговечности;
д) обобщающий анализ результатов контроля, исследования металла и расчетов на прочность с установлением назначенного ресурса или срока службы.
При проведении работ по диагностированию следует руководствоваться ФНиП №116 от 25.03.2014 и РД 10-577-03 «Типовая инструкция по контролю металла и продлению срока службы основных элементов котлов, турбин и трубопроводов тепловых электростанций».
13.3. Объём, периодичность и критерии оценки технического состояния деталей, узлов и арматуры в целом приведены в пункте 3 настоящего руководства по эксплуатации.
13.4. По результатам диагностирования эксплуатирующей организацией принимается решение о дальнейшей эксплуатации арматуры или проведении ремонта.
14. КОМПЛЕКТНОСТЬ
В комплект поставки входит:
- регулирующий игольчатый клапан;
- паспорт на клапан;
- руководство по эксплуатации – 2 экземпляра на партию изделий, отправляемых в один адрес;
- расчет на прочность (по требованию потребителя);
- копия обоснования безопасности (по требованию потребителя).
Паспорт поставляется в одном экземпляре с каждым изделием DN ≥ 50. Для изделий арматуры DN < 50 предусмотрен один паспорт на партию. Партией считается количество изделий до 50 штук, единовременно отправляемых в один адрес.
15. НАИМЕНОВАНИЕ, МЕСТОНАХОЖДЕНИЕ И КОНТАКТНАЯ ИНФОРМАЦИЯ ИЗГОТОВИТЕЛЯ
Изготовитель продукции: ООО «Барнаульский котельный завод».
Почтовый адрес: 656023, Россия, г. Барнаул, пр. Космонавтов, 6Э.
Телефон: (3852) 22-32-67, 22-32-68, факс: 22-32-86.
E-mail: bkz@bkzn.ru
www.bkzn.ru