Руководство на Клапаны запорные DN 80 типа 1с
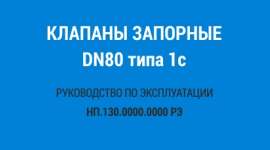
Предназначено для ознакомления обслуживающего персонала с устройством и работой клапанов (вентилей) запорных DN 80 типа 1с НП.130.0000.0000 РЭ
Настоящее руководство по эксплуатации (далее по тексту – РЭ) предназначено для ознакомления обслуживающего персонала с устройством и работой клапанов (вентилей) запорных DN 80 типа 1с, использующихся в качестве запорных устройств в трубопроводах воды и водяного пара теплоэнергетических установок, а также служит руководством по их монтажу и эксплуатации.
В связи с постоянной работой по совершенствованию клапанов в конструкцию могут быть внесены незначительные изменения, не отраженные в данном РЭ.
Пример наименования при заказе изделия арматуры:
Клапан (вентиль) запорный DN 80 DN 80 1с-8-2 ТУ 2913-001-15365247-2004.
Почтовый адрес: 656023, Россия, г.Барнаул, пр.Космонавтов, 6Э.
Телефон: (3852) 22-32-67, 22-32-68, факс: 22-32-86
www.bkzn.ru
E-mail: bkz@bkzn.ru
СОДЕРЖАНИЕ
- Описание и работа
- Использование по назначению
- Техническое обслуживание
- Возможные неисправности и способы их устранения
- Порядок разборки и сборки клапанов
- Назначенные показатели
- Перечень критических отказов, возможные ошибочные действия персонала, которые приводят к инциденту или аварии
- Действия персонала в случае инцидента, критического отказа или аварии
- Критерии предельных состояний
- Сведения о квалификации обслуживающего персонала
- Показатели энергетической эффективности
- Правила хранения и транспортирования
- Указания по выводу из эксплуатации и утилизации
- Диагностирование
-
Комплектность
1 ОПИСАНИЕ И РАБОТА
1.1 Клапаны (вентили) запорные DN 80 типа 1с применяются для перекрытия потока рабочей среды в трубопроводе. Использование клапанов в качестве регулирующих устройств не допускается.
1.2 Клапаны (вентили) запорные DN 80 изготавливаются следующих исполнений:
- 1с-7 – с маховиком,
- 1с-8 – с цилиндрическим редуктором,
- 1с-9 – с коническим редуктором,
- 1с-8-2Э – с электроприводом.
Основные технические данные приведены в таблице 1. Устройство клапанов показано на рисунках 1, 2, 3, 4, габаритные и присоединительные размеры – в таблице 2.
1.3 Клапаны (вентили) запорные служат для полного закрытия (открытия) потока рабочей среды путем возвратно-поступательного перемещения запорного органа вдоль оси потока, перпендикулярно плоскости седла. Открывание клапанов производится полностью до упора, а закрывание – с моментом, не превышающим указанного в таблице 1.
1.4 Управление клапаном осуществляется непосредственно маховиком 8 (рис. 1) или через редукторы с цилиндрическим или коническим зацеплением (рис. 2, 3). Управление клапаном 1с-8-2Э осуществляется электроприводом типа ЭП-З-300 производства ОАО «БЕТРО» г. Бердск или ПЭМБ-2 производства ОАО «ЗЭиМ» г. Чебоксары, или Н-Б1-07 производства ОАО «Тулаэлектропривод» и имеют возможность комплектации с другими приводами соответствующих параметров. К валику редуктора может быть присоединен посредством шарнира ручной дистанционный привод или колонковый электропривод.
Закрытие клапанов происходит при вращении маховика по часовой стрелке.
1.5 Клапаны состоят из следующих основных узлов и деталей:
- литого корпуса 1 с уплотнительной наплавкой;
- литой крышки 2;
- тарелки 3 с уплотнительной наплавкой;
- шпинделя 4;
- узла сальника 5;
- мостика грундбуксы 6;
- втулки 7;
- маховика 8 (рис. 1);
- редуктора с цилиндрическим зацеплением (рис. 2);
- редуктора с коническим зацеплением (рис. 3);
- электропривода (рис. 4).
1.6 Материалы основных деталей клапанов запорных:
- Корпус – сталь 25Л ОСТ 108.961.03-79 с уплотнительной наплавкой ВПН-1.
- Крышка – сталь 25Л ОСТ 108.961.03-79.
- Тарелка – сталь 20 ГОСТ 1051-88 с уплотнительной наплавкой 20Х13.
Допускается изготовление корпуса и крышки из стали 20ГСЛ по ОСТ 108.961.03-79.
Таблица 1 – Основные технические параметры
Рабочая среда – вода, пар.
Вид привода:
- М – маховик
- Ц – цилиндрический редуктор
- К – конический редуктор
- Э – электропривод
Таблица 2 – Основные габаритные и присоединительные размеры
1.7 Порядок обжатия сальникового уплотнения
а) Провести обжатие сальникового уплотнения усилием Q, создаваемым крутящим моментом затяжки болтов не менее значений, указанных в Таблице 3;
б) Сделать 5-6 циклов полного хода для распределения усилия затяжки по высоте сальникового пакета;
в) Вновь обжать сальниковый пакет усилием Q;
г) Повторить п.п. б) и в) до прекращения ослабления затяжки болтов после п. б).
Таблица 3 – Необходимое усилие обжатия комплекта уплотнительных сальниковых колец
Рисунок 1 – Клапан (вентиль) запорный 1с-7-1
1 – Корпус
2 – Крышка
3 – Тарелка
4 – Шпиндель
5 – Кольцо сальниковое
6 – Мостик грундбуксы
7 – Втулка резьбовая
8 – Маховик
9 – Гайка М24 52х36х8-ГФ1-5 шт.
10 – Гайка М20
Рисунок 2 – Клапан (вентиль) запорный 1с-8-2
1 – Корпус
2 – Крышка
3 – Тарелка
4 – Шпиндель
5 – Кольцо сальниковое
6 – Мостик грундбуксы
7 – Втулка резьбовая
8 – Маховик
9 – Корпус редуктора
10 – Гайка М20
11 – Колесо зубчатое
12 – Винт установочный
Рисунок 3 – Клапан (вентиль) запорный 1с-9-2
Рисунок 4 – Клапан (вентиль) запорный 1с-8-2ЭН
1.8 На корпусе клапана должна быть нанесена маркировка (Рисунок 5). Маркировка должна содержать следующие сведения:
- наименование и (или) обозначение типа, марки, модели оборудования;
- параметры и характеристики, влияющие на безопасность (давление номинальное (PN, кгс/см²) или давление рабочее (Pр, кгс/см²) и температура (t, °С));
- диаметр номинальный;
- наименование марки материала, из которого изготовлен корпус, или его условное обозначение;
- товарный знак или наименование предприятия-изготовителя;
- заводской номер изделия по системе нумерации предприятия-изготовителя;
- дата изготовления;
- «Сделано в России» (для экспорта);
- стрелку-указатель направления потока среды (в случае регламентированного направления среды);
- клеймо ОТК;
- знак обращения продукции на рынке государств-членов ТС (допускается располагать в эксплуатационной документации).
Клапаны отправляются заказчику с заглушенными патрубками и плотно закрытым затвором, упакованными в соответствии с требованиями договора, контракта, технической документации и технологических инструкций предприятия-изготовителя.
Рисунок 5 – Место нанесения маркировки
2 ИСПОЛЬЗОВАНИЕ ПО НАЗНАЧЕНИЮ
2.1 Эксплуатационные ограничения
2.1.1 Требования безопасности на всех стадиях эксплуатации клапанов должны соответствовать Федеральным нормам и правилам в области промышленной безопасности:
- «Правила промышленной безопасности опасных производственных объектов, на которых используется оборудование, работающее под избыточным давлением», утвержденные приказом Федеральной службы по экологическому, технологическому и атомному надзору от 25.03.2014 г. №116;
- Технический регламент Таможенного союза «О безопасности оборудования, работающего под избыточным давлением» (ТР ТС 032/2013), принятый Решением Совета Евразийской экономической комиссии от 2 июля 2013 г. №41;
- Технический регламент Таможенного союза «О безопасности машин и оборудования», утвержденный Решением Комиссии Таможенного союза от 18.10.2011 г. №823 (ТР ТС 010/2011).
2.1.2 Клапаны (вентили) запорные могут устанавливаться как на горизонтальных, так и на вертикальных участках трубопровода с направлением потока среды "под тарелку". При установке клапана с электроприводом на вертикальном трубопроводе с горизонтальным расположением шпинделя необходимо установить опору под электропривод.
2.1.3 В номинальном режиме скорость воды в трубопроводах, где установлены клапаны, не должна превышать 5 м/с, пара – 60 м/с.
2.1.4 Клапаны рекомендуется эксплуатировать в закрытых помещениях с параметрами окружающей среды:
- температура от -40˚С до +70 ºС;
- относительная влажность до 95 %.
Для эксплуатации при температуре ниже 0˚С проектом должен быть предусмотрен дополнительный обогрев и изоляция подводящего трубопровода для исключения замерзания рабочей среды в клапане.
2.1.5 В местах установки клапанов должен быть обеспечен свободный доступ для их обслуживания и ремонта без вырезки из трубопровода.
2.1.6 Присоединение клапанов к трубопроводу должно производиться при помощи сварки.
2.1.7 Перед монтажом клапана необходимо произвести его расконсервацию:
- снять заглушки с патрубков;
- удалить консервационную смазку уайт-спиритом ГОСТ 3134-78;
- тщательно осмотреть и очистить все детали от загрязнений;
- смазать контактирующую с сальником поверхность шпинделя графитной смазкой марки ГС-1 или ГС-2 ГОСТ 8295-73;
- проверить плавность хода шпинделя при открывании и закрывании.
2.1.8 Произвести гидравлическое испытание на герметичность сальникового уплотнения и затвора.
2.1.9 Трубопровод перед монтажом клапана должен быть тщательно очищен от грязи, окалины, сварочного грата и других посторонних предметов.
2.1.10 Произвести установку клапана в трубопровод при плотно закрытом затворе.
2.1.11 Работа клапана в кавитационном режиме недопустима.
2.1.12 Для обеспечения безопасной работы клапанов запорных КАТЕГОРИЧЕСКИ ЗАПРЕЩАЕТСЯ:
- ЭКСПЛУАТИРОВАТЬ КЛАПАНЫ НА ПАРАМЕТРАХ, ПРЕВЫШАЮЩИХ УКАЗАННЫЕ В ДОКУМЕНТАЦИИ;
- ПРОИЗВОДИТЬ РАБОТЫ ПО УСТРАНЕНИЮ ДЕФЕКТОВ ПРИ НАЛИЧИИ ДАВЛЕНИЯ В ТРУБОПРОВОДЕ;
- НАСТРАИВАТЬ МУФТУ ОГРАНИЧЕНИЯ КРУТЯЩЕГО МОМЕНТА ЭЛЕКТРОПРИВОДА НА ВЕЛИЧИНУ, ПРЕВЫШАЮЩУЮ УКАЗАННУЮ В НАСТОЯЩЕМ РУКОВОДСТВЕ;
- ЭКСПЛУАТИРОВАТЬ КЛАПАНЫ СО ВСТРОЕННЫМ ЭЛЕКТРОПРИВОДОМ ПРИ НЕВЫСТАВЛЕННЫХ КОНЦЕВЫХ И ПУТЕВЫХ ВЫКЛЮЧАТЕЛЯХ ПОЛОЖЕНИЯ «ОТКРЫТО» И «ЗАКРЫТО», БЕЗ НАСТРОЙКИ МУФТЫ ОГРАНИЧЕНИЯ КРУТЯЩЕГО МОМЕНТА НА ЭЛЕКТРОПРИВОДЕ.
2.2 Эксплуатация во взрывоопасной среде
2.2.1 Клапаны имеют уровень взрывозащиты Gb и допускают применение во взрывоопасных газовых средах в помещениях, кроме подземных выработок шахт, рудников и их наземных строений, где возможно возникновение взрывоопасной среды, создаваемой смесями воздуха и газов, паров, туманов.
2.2.2 В качестве подтверждения применения во взрывоопасной среде на клапане должна быть нанесена маркировка «IIGb c 450», что означает:
- оборудование группы II, уровень взрывозащиты Gb;
- вид взрывозащиты – конструкционная безопасность («с»);
- применение во взрывоопасной газовой среде с температурой поверхности клапана до 450 ºС.
Температура поверхности соответствует температуре среды внутри трубопровода и определяется разработчиком проекта трубопровода из условий взрывобезопасности.
2.2.3 В случае применения клапана с электрическим приводом последний должен быть во взрывозащищённом исполнении с соответствующим требованиям проекта уровнем защиты.
2.3 Монтаж клапанов запорных
2.3.1 Монтаж клапанов должен производиться монтажной организацией согласно документации, разработанной проектно-конструкторской организацией, с учётом требований РД 153-34.1-003-01 «Сварка, термообработка и контроль трубных систем котлов и трубопроводов при монтаже и ремонте энергетического оборудования» и настоящего РЭ.
2.3.2 Клапаны отправляются на место монтажа с плотно закрытым затвором и заглушенными патрубками.
2.3.3 Транспортирование клапанов к месту монтажа должно производиться с соблюдением всех предосторожностей, гарантирующих защиту от поломок и повреждений.
2.3.4 Перед установкой клапанов в трубопровод при закрытом затворе необходимо:
- снять заглушки;
- очистить внутренние полости клапана от возможного загрязнения;
- законсервированные наружные поверхности клапана протереть ветошью, смоченной уайт-спиритом (нефрасом-С155/200 ГОСТ 3134-78) или нефрасом-С50/170 ГОСТ 8505-80;
- затем обработать раствором моющего дезинфицирующего средства «МДС» вид Б или В ТУ 12-РФ-938-95 либо раствором моющего технического средства МС-37 ТУ РСФСР 964-92 до полного удаления консервационных смазок.
Протереть насухо. Расконсервацию внутренних поверхностей, законсервированных контактным ингибитором коррозии – загущенным раствором нитрита натрия, произвести путём промывки их водой с использованием протирочного материала с последующей сушкой до полного удаления влаги с поверхностей.
2.3.5 Клапаны, имеющие внешние признаки повреждений (забита резьба, погнут шпиндель и др.), должны быть подвергнуты ревизии.
2.3.6 Монтаж и наладку арматуры должны осуществлять специализированные организации, имеющие статус юридического лица и организационную форму, соответствующую требованиям законодательства Российской Федерации, а также индивидуальные предприниматели (далее - специализированные организации).
2.3.7 Монтаж с применением сварки и термической обработки должен проводиться по технологии и рабочим чертежам, разработанным на основании ФНП «Требования к производству сварочных работ на опасных производственных объектах» (далее ФНП) и РД 153–34.1–003–01 «Сварка, термообработка и контроль трубных систем котлов и трубопроводов при монтаже и ремонте энергетического оборудования» (далее РТМ–1с).
2.3.8 При монтаже должна быть применена технология сварки, аттестованная в соответствии с установленными требованиями.
2.3.9 Для выполнения сварки должны быть применены исправные установки, аппаратура и приспособления, обеспечивающие соблюдение требований технологической документации.
2.3.10 К производству работ по сварке и прихватке элементов оборудования, предназначенных для работы под давлением, допускают сварщиков, имеющих удостоверение на право выполнения данных сварочных работ. Сварщики должны выполнять сварочные работы только тех видов, к проведению которых согласно удостоверению, они допущены.
2.3.11 Руководство работами по сборке, сварке и контролю качества сварных соединений должно быть возложено на специалиста, прошедшего в установленном порядке аттестацию.
2.3.12 Работоспособность привода арматуры, имеющей механический или электрический привод, проверять до передачи в монтаж.
2.3.13 Трубопроводную арматуру монтировать в закрытом состоянии. Фланцевые и приварные соединения арматуры выполнять без натяжения трубопровода. Во время сварки приварной арматуры её затвор или клапан приоткрывается, чтобы предотвратить заклинивание его при нагревании корпуса. Если сварка проводится без подкладных колец, арматуру по окончании сварки можно закрыть только после её внутренней очистки.
2.3.14 Технологическая документация должна содержать указания по технологии сварки металла (в том числе и по прихватке), применению присадочных материалов, видам и объёму контроля, а также по предварительному и сопутствующему подогреву и термической обработке. Технологическая документация должна соответствовать требованиям ФНП и РТМ–1с.
2.3.15 Перед началом сварки должно быть проверено качество сборки соединяемых элементов, а также состояние стыкуемых кромок и прилегающих к ним поверхностей. При сборке не допускается подгонка кромок ударным способом или местным нагревом.
2.3.16 Подготовка кромок и поверхностей под сварку должна быть выполнена механической обработкой либо путем термической резки или строжки (кислородной, воздушно-дуговой, плазменно-дуговой) с последующей механической обработкой (резцом, фрезой, абразивным инструментом). Глубина механической обработки после термической резки (строжки) должна быть указана в технологической документации в зависимости от восприимчивости конкретной марки стали к термическому циклу резки (строжки).
2.3.17 При сборке стыковых соединений труб с односторонней разделкой кромок и свариваемых без подкладных колец и подварки корня шва смещение (несовпадение) внутренних кромок не должно превышать значений, установленных в технологической документации.
2.3.18 Кромки деталей, подлежащих сварке, и прилегающие к ним участки должны быть очищены от окалины, краски, масла и других загрязнений в соответствии с требованиями технологической документации.
2.3.19 Приварка и удаление вспомогательных элементов (сборочных устройств, временных креплений) должны быть произведены в соответствии с указаниями чертежей и технологической документации по технологии, исключающей образование трещин и закалочных зон в металле. Приварку этих элементов должен выполнять сварщик, допущенный к проведению сварочных работ на данном оборудовании.
2.3.20 Прихватка собранных под сварку элементов должна быть выполнена с использованием тех же сварочных материалов, которые будут применены (или допускаются к применению) для сварки данного соединения.
2.3.21 Прихватки при дальнейшем проведении сварочных работ удаляют или переплавляют основным швом.
2.3.22 Сварные соединения элементов, с толщиной стенки более 6 мм подлежат маркировке (клеймению), позволяющей установить фамилию сварщика, выполнившего сварку. Система маркировки указывается в технологической документации. Способ маркировки должен исключать наклеп, подкалку или недопустимое утонение толщины металла и обеспечить сохранность маркировки в течение всего периода эксплуатации оборудования.
2.3.23 Необходимость и способ маркировки сварных соединений с толщиной стенки 6 мм и менее устанавливается требованиями технологической документации.
3 ТЕХНИЧЕСКОЕ ОБСЛУЖИВАНИЕ
3.1 К эксплуатации, ремонту и обслуживанию клапанов допускается персонал, изучивший их устройство, правила техники безопасности и требования настоящего руководства, аттестованный на право выполнения работ по обслуживанию запорной арматуры.
3.2 Во время открывания и закрывания клапана пользоваться дополнительными рычагами не допускается.
3.3 Клапаны должны допускать возможность теплоизолирования. Температура на поверхности теплоизоляции не должна превышать 50°С.
3.4 Закрытие клапанов должно производиться вращением маховика по часовой стрелке. Величина крутящего момента на маховике не должна превышать указанной в таблице 1.
3.5 Порядок технического обслуживания:
3.5.1 Техническое обслуживание вентилей необходимо проводить в объёме таблицы 4.
Таблица 4 – Порядок технического обслуживания
3.6 Техническое освидетельствование:
3.6.1 Клапаны должны подвергаться перед пуском в работу и в процессе эксплуатации следующим видам технического освидетельствования: наружному осмотру и гидравлическому испытанию совместно с трубопроводом.
3.6.2 Техническое освидетельствование клапанов должно проводиться лицом, ответственным за исправное состояние и безопасную эксплуатацию.
3.6.3 Наружный осмотр клапанов проводить в объёме таблицы 5.
3.6.4 Гидравлические испытания клапанов проводить перед пуском в эксплуатацию после монтажа, ремонта, связанного со сваркой, а также при пуске трубопроводов после нахождения их в состоянии консервации свыше трех лет тем же давлением, что и трубопроводы.
Таблица 5 – Наружный осмотр
4 ВОЗМОЖНЫЕ НЕИСПРАВНОСТИ И СПОСОБЫ ИХ УСТРАНЕНИЯ
5 ПОРЯДОК РАЗБОРКИ И СБОРКИ КЛАПАНА
5.1 Разборка клапана с маховиком производится в следующем порядке:
- снять маховик 8, предварительно отвинтив гайку 9;
- снять крышку 2 вместе с мостиком грундбуксы 6, предварительно отвинтив гайки 10;
- вынуть шпиндель 4 вместе с тарелкой 3, разобрать;
- разобрать крышку 2, отвинтив болты откидные, снять мостик грундбуксы 6, вывинтить втулку 7, вынуть узел сальника 5;
- проверить состояние рабочих поверхностей шпинделя 4, корпуса 1, тарелки 3.
Если обнаружены дефекты, устранить их.
5.2 Разборка клапанов с цилиндрическим или коническим редуктором производится в следующем порядке:
- снять муфту, предварительно выбив штифт, снять маховик 8;
- снять крышку корпуса редуктора 9, предварительно вывинтив винты;
- снять колесо зубчатое 11, предварительно вывинтив винт;
- снять корпус редуктора 9 вместе с валиком и шестерней, предварительно вывинтив винты установочные 12;
- снять крышку 2 вместе с мостиком грундбуксы 6, ходовой втулкой 7 и шпинделем, предварительно отвинтив гайки 10;
- снять тарелку 3 и вывернуть шпиндель 4;
- разобрать крышку 2, отвинтив болты откидные, снять мостик грундбуксы 6, вынуть ходовую втулку 7 вместе с подшипниками, предварительно вывернув кольцо упорное, вынуть узел сальника 5;
- проверить состояние рабочих поверхностей шпинделя 4, корпуса 1, тарелки 3.
Если обнаружены дефекты и забоины, устранить их.
5.3 Сборку клапана производить в последовательности, обратной разборке, предварительно тщательно очистив от грязи, пыли и других загрязнений.
6 НАЗНАЧЕННЫЕ ПОКАЗАТЕЛИ
6.1. Клапаны (вентили) запорные относятся к классу ремонтируемых, восстанавливаемых изделий с регламентированной дисциплиной и назначенной продолжительностью эксплуатации. При эксплуатации допускаются профилактические осмотры и, при необходимости, текущие ремонты (замена сальникового уплотнения, смазка и т. п.), но не реже чем через 10 000 часов работы.
6.2. Изделия арматуры должны обеспечивать показатели надежности:
- средний срок службы до первого капитального ремонта — не менее 4 лет;
- средняя наработка на отказ — не менее 500 циклов.
6.3. Изделия арматуры должны обеспечивать показатели безопасности:
- назначенный срок службы корпусных деталей — не менее 25 лет;
- назначенный срок службы выемных частей и комплектующих — не менее 10 лет (75 000 ч);
- назначенный ресурс за 4 года (30 000 ч) — не менее 1 000 циклов;
- назначенный срок хранения — 3 года.
При достижении указанных показателей эксплуатация арматуры должна быть прекращена независимо от ее технического состояния. Дальнейшая эксплуатация возможна только по решению комиссии, проведшей экспертное обследование в установленном порядке.
7 ПЕРЕЧЕНЬ КРИТИЧЕСКИХ ОТКАЗОВ И ОШИБОК ПЕРСОНАЛА, ПРИВОДЯЩИХ К ИНЦИДЕНТАМ
7.1. Возможные критические отказы:
- потеря прочности корпусных деталей и сварных соединений;
- потеря плотности материалов корпусных деталей и сварных соединений;
- потеря герметичности по уплотнениям неподвижных и подвижных соединений;
- утечки в клапане, превышающие установленные нормы;
- невыполнение функций "открытие" или "закрытие";
- несоответствие времени срабатывания;
- увеличение крутящего момента более чем на 10% от установленного.
Критичность отказов определяется проектировщиком системы в соответствии с ГОСТ Р 55018-2012 и ГОСТ 27.310.
7.2. Ошибки персонала, приводящие к инциденту или аварии:
- допуск к обслуживанию неподготовленного персонала;
- превышение паспортных параметров эксплуатации;
- использование неподходящих материалов при ремонте;
- работы по устранению дефектов под давлением;
- нарушение условий эксплуатации;
- использование арматуры не по назначению.
8 ДЕЙСТВИЯ ПЕРСОНАЛА В СЛУЧАЕ ИНЦИДЕНТА
При аварийной ситуации необходимо отключить подачу среды на клапан, определить причину инцидента и принять решение о ремонте или утилизации.
9 КРИТЕРИИ ПРЕДЕЛЬНЫХ СОСТОЯНИЙ
К предельным состояниям арматуры относятся:
- нарушение целостности корпусных деталей (утечки);
- недопустимое изменение размеров элементов;
- потеря герметичности разъемных соединений;
- трещины на основных деталях;
- шум от протекания среды или обмерзание корпуса;
- увеличение крутящего момента сверх норм.
-
КВАЛИФИКАЦИЯ ОБСЛУЖИВАЮЩЕГО ПЕРСОНАЛА
Персонал должен соответствовать квалификационным требованиям, проходить проверку знаний и аттестацию согласно нормативным документам. Работы по сварке и контролю должны выполняться сертифицированными специалистами.
11 ПОКАЗАТЕЛИ ЭНЕРГЕТИЧЕСКОЙ ЭФФЕКТИВНОСТИ
Основной показатель энергетической эффективности запорных клапанов — коэффициент гидравлического сопротивления ().
12 ПРАВИЛА ХРАНЕНИЯ И ТРАНСПОРТИРОВАНИЯ
12.1. Хранение:
- клапаны хранятся на стеллажах или подставках;
- патрубки заглушены;
- консервация выполняется согласно ГОСТ 9.014-78;
- переконсервация каждые 3 года.
12.2. Транспортирование:
- соответствие ГОСТ 23170-78;
- возможна перевозка любым видом транспорта;
- контроль наличия заглушек в процессе транспортировки.
13 ВЫВОД ИЗ ЭКСПЛУАТАЦИИ И УТИЛИЗАЦИЯ
13.1. По окончании срока службы клапаны подлежат утилизации. 13.2. Утилизация не распространяется на электроприводы и комплектующие. 13.3. Арматура утилизируется при невозможности или нецелесообразности ремонта. 13.4. Ответственные лица должны контролировать процесс утилизации. 13.5. Утилизация проводится способом, исключающим восстановление. 13.6. Перед утилизацией арматура должна быть отключена и освобождена от рабочей среды.
14 ДИАГНОСТИРОВАНИЕ
14.1. Техническое диагностирование проводят специализированные организации с лицензией в следующих случаях:
- по истечении срока службы;
- при обнаружении дефектов;
- в иных предусмотренных случаях.
14.2. Комплекс диагностических мероприятий включает:
- анализ документации и контрольных данных;
- оценку прочности и остаточного ресурса;
- обобщение результатов и назначение дальнейшего срока службы.
14.3. Периодичность диагностики приведена в разделе 3 руководства.
14.4. По результатам диагностики принимается решение о продолжении эксплуатации или ремонте.
15 КОМПЛЕКТНОСТЬ
В комплект поставки входит:
- клапан запорный;
- паспорт на клапан;
- руководство по эксплуатации – 2 экземпляра на партию изделий, отправляемых по одному адресу;
- расчет на прочность (при наличии запроса от потребителя);
- копия обоснования безопасности (при наличии запроса от потребителя).
Партией считается до 50 изделий, отправляемых одновременно по одному адресу.